The cement steel silo is a closed industrial silo for storing materials. In daily use, the loading and unloading of cement steel silos should strictly follow the operating procedures and requirements. Otherwise, it may lead to safety accidents.
Next, we will introduce to you the precautions for the loading and unloading process of cement silos.
Precautions for Loading Process
Before the cement steel silo is loaded for the first time, it is necessary to take forced drying measures such as ventilation prevent compaction. At the same time, it is necessary to clean the silo to prevent blockage of the pipeline due to debris, concrete blocks, or wood boards left in the bottom and the storage chute of the silo.
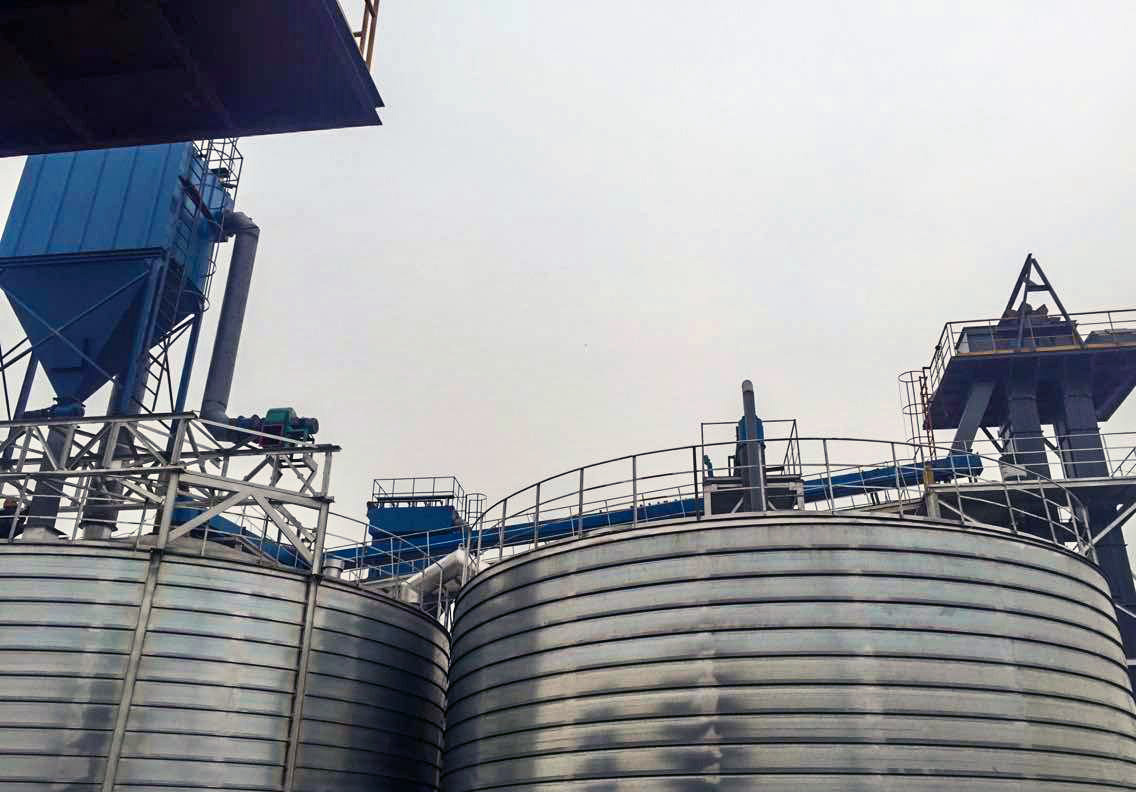
Before the dust collector on the silo roof is turned on, the air conditioning duct on the silo roof should be checked first. The dust collector can only be opened after confirming that the air conditioning duct is open. Otherwise, serious accidents such as the steel silo being sucked may occur. If a differential pressure safety valve is used, it must be ensured that the valve is sensitive and reliable. So that when a slight negative pressure occurs in the chamber, it can be opened in time.
Impurities should be prevented from mixing with the warehousing cement, or it may cause unnecessary troubles when unloading. To avoid iron slag entering, the ground cement should be inspected by iron removal equipment before being loaded into the silo.
Use a dry gas source. The inspectors should regularly check the gas source to prevent the stagnant water from entering the chamber with the airflow, which would cause condensation in the fluidized pipeline, and affect the fluidized unloading.
The gas return check valve should be ensured to be safe and reliable. When the loading is stopped, the air supply valve of the transmitter must be turned off without air pressure in the air supply line. In this way, it is possible to prevent the air supply pipeline from being blocked due to the return of ash.
Users need to check the operation of the chute fan regularly to ensure that it runs smoothly, without vibration. Otherwise, it will have an adverse effect on the silo structure. At the same time, users should also timely check the operation of the ash unloader valve of the dust collector on the silo top to ensure that the unloading system is good, so as to prevent the top load from being aggravated by a large amount of accumulated dust in the dust collector.
The sealing condition of the holes such as the feed inlet and the measuring hole of the cement silo should be checked in advance. Make sure they are well sealed and no water can enter the silo. And do not add new holes or freeloads on the silo roof and the silo body.
The initial loading of the cement silo must be completed in at least three batches. The first loading amount cannot exceed 60% of the silo capacity, and it needs to stand for 20 days before the second loading; the second loading volume cannot exceed 90% of the silo capacity, and then wait another 20 days, the silo can be fully filled by the third loading. The purpose is to prevent the silo from tilting during the loading process.
When filling the cement silo, we need to observe the sinking condition of the silo body. Technicians would generally formulate a guidebook for loading and unloading according to different geological foundations so that we could follow the guidebook to control the progress of the loading and make observations of the sedimentation values at the same time. If there are two silos loading at the same time, we need to ensure that their load rates are exactly the same, so as to avoid inconsistent settlement of the two silos which could lead to excessive truss tension and truss bending.
Precautions for Unloading Process
Before the unloading, the cement density in the cement silo must be ensured to be uniform. If the cement in the silo is not uniform and there is a phenomenon that the center of gravity deviates, then when the cement is unloaded, the cement silo may be deflected.
Matters Need to Be Checked in Preparatory Work Before Unloading
1) Check whether the pressure of the Roots blower reaches the corresponding pressure. Open the Roots blower vent valve (to prevent the motor from overheating and burning). Start the Roots blower and adjust the Roots blower control valve. The operating pressure of the Roots blower is adjusted to ≥ 0.784Mpa. When the material level is high, the Roots blower does not have to be turned on. If the discharge is not smooth, then we can open the Roots blower to loosen the material.
2) Check the closure of the manual ball valve around the silo body (usually the outer zone is closed and the inner zone is opened).
3) Check that the discharge valve is open. The opening during the early period should be appropriately smaller and then adjusted according to the discharge conditions.
4) Check whether the power supply control cabinet of the unloading system is ready and whether the feeding cycle switch is adjusted to the right position. If the system is ready, then we can activate the automatic unloading program. Otherwise, we should unload manually.
5) Check the vulcanization rod homogenization system in the cement silo. A plurality of vulcanization rods are generally set in the cement silo, and the silo area is divided into several unloading zones by each vulcanization rod. Each discharge area is equipped with its own solenoid valve. The vulcanizing rod in each discharge zone is an independent unloading system. Even if a vulcanizing rod in a zone fails, it will not affect the work of other vulcanization rods.
Conclusion
Cement steel silos are very durable containers for cement storage, but they could still be damaged by wrong operations. Loading and unloading a cement steel silo following these instructions would effectively decrease the rate of safety accident.
Flyer Steel Silo provides high-quality storage system design and construction service worldwide. Please message us if you have any questions about silo storage!